H2S Monitor Calibration - Ensuring Safety in Hazardous Environments
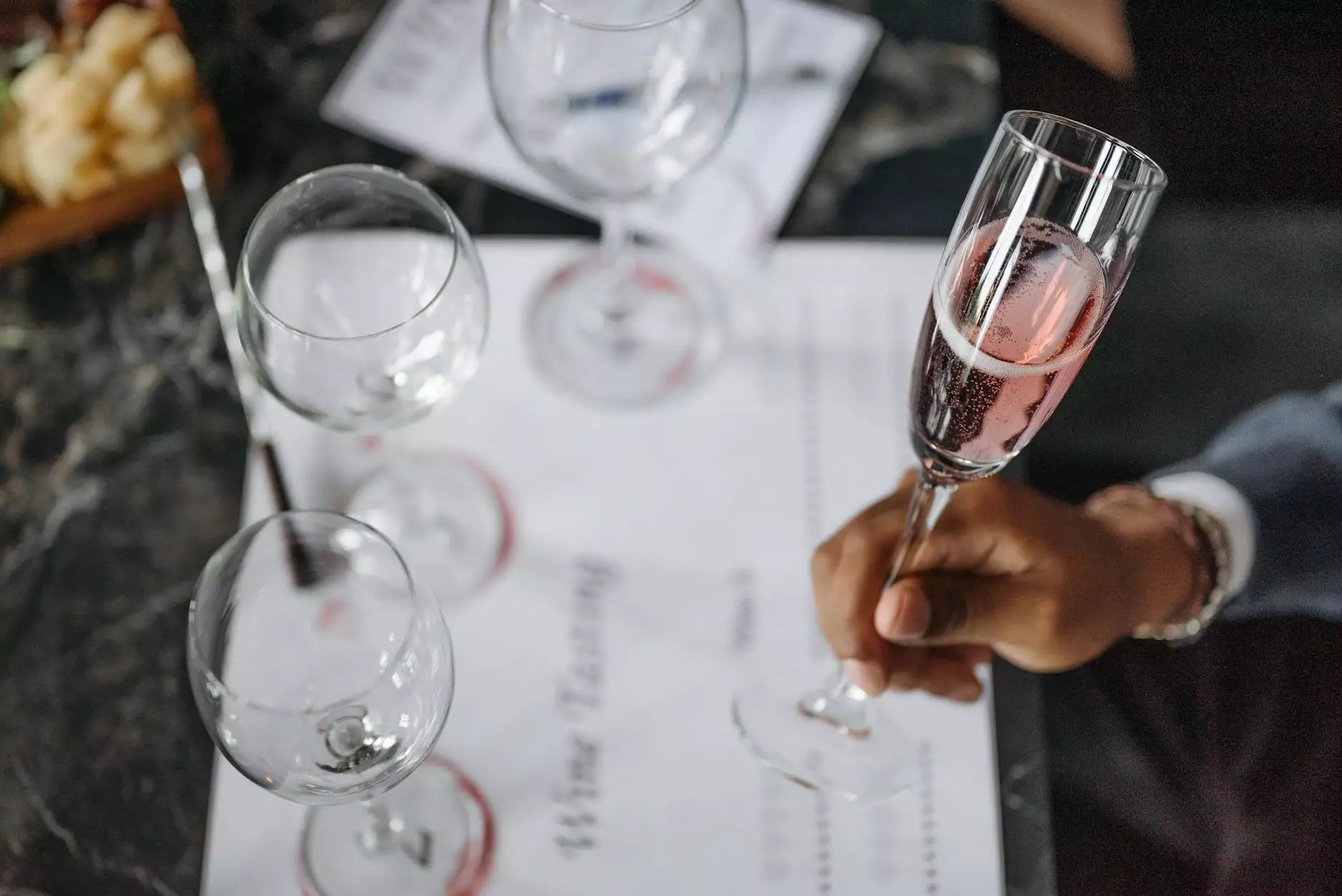
The danger of hydrogen sulfide (H2S) gas in industrial operations cannot be overlooked. As a highly toxic substance, accurate monitoring of H2S levels is critical for the safety of workers and the integrity of operational processes. One of the fundamental aspects of effective monitoring is H2S monitor calibration. This article delves deep into the significance of calibrating H2S monitors, methods of calibration, best practices, and how proper calibration can impact overall safety in hazardous workplaces.
Understanding H2S and Its Risks
Hydrogen sulfide is a colorless gas with a characteristic odor of rotten eggs. It is produced by the decomposition of organic matter and is present in various industrial sectors such as oil and gas, sewage treatment, and mining. The risks associated with H2S include:
- Toxicity: H2S can be fatal at concentrations above 100 parts per million (ppm).
- Flammability: It is highly flammable and can lead to explosions in certain conditions.
- Health Effects: Low levels can cause irritation of the eyes, throat, and respiratory system.
The Importance of H2S Monitor Calibration
Calibration is a crucial process that ensures H2S monitors provide accurate and reliable readings. Incorrect measurements can lead to catastrophic consequences, including worker exposure or false sense of security. Here’s why H2S monitor calibration is vital:
1. Compliance with Safety Regulations
Many industries are governed by strict regulations regarding the monitoring of toxic gases. Regular calibration of H2S monitors helps businesses stay compliant with OSHA (Occupational Safety and Health Administration) standards and other relevant regulations.
2. Enhancing Worker Safety
Accurate readings from calibrate monitors allow for timely alerts to dangerous gas levels, enabling workers to take necessary precautions. This is particularly important in hazardous environments where H2S is a risk.
3. Minimizing Operational Downtime
Properly calibrated instruments reassure operators that they are functioning accurately, potentially reducing operational downtime due to false alarms or mishaps caused by equipment failure.
How to Calibrate H2S Monitors
Calibrating H2S monitors can be approached in various ways. It typically involves exposing the monitor to a known concentration of H2S gas to adjust the reading to align with that concentration. Below are the primary methods used for H2S monitor calibration:
1. Bump Testing
Bump testing is a quick way to ensure that the monitor responds correctly to H2S levels. In this method, a test gas cylinder with a known concentration of H2S is used. After applying the gas to the monitor, you can verify if it alarms at the appropriate levels.
2. Factory Calibration
For guarantees of precision, sending equipment back to the manufacturer for recalibration is an option worth considering. This involves extensive testing and adjustments. Many companies offer factory calibration services, ensuring that every component of the monitor is functioning correctly.
3. Field Calibration
This method provides a convenient option for on-site calibration. With the help of calibration kits, the user can adjust the monitor to account for any discrepancies while still in the field. It's a practical option for facilities that operate in multiple environments.
Best Practices for H2S Monitor Calibration
To ensure the highest standards of safety and accuracy in H2S monitoring, adhering to best practices during calibration is essential. Here are some recommended practices:
1. Regular Calibration Schedule
Establish a regular calibration schedule based on the manufacturer's recommendations and the usage of the monitor. It is commonly suggested to perform a bump test at the beginning of each shift and a full calibration on a monthly basis.
2. Keep Records
Maintain detailed records of all calibration activities. Logging test results, dates of testing, and maintenance performed can serve as a useful reference and is often required for compliance audits.
3. Use Quality Calibration Gases
Always use calibration gases that meet the required purity standards. Impurities in the calibration gas can lead to faulty readings, negating the purpose of the calibration.
4. Train Personnel
Ensure that all personnel responsible for calibration are adequately trained on the procedures and understand the importance of accurate monitoring. Regular training updates can enhance their skills and knowledge on the latest technologies.
The Future of H2S Monitoring Technology
As technology continues to evolve, so does the field of gas detection and monitoring. Innovations such as smart sensors and IoT integration are becoming more prevalent, providing the ability to monitor H2S levels remotely and in real-time. These advancements offer potential for improved safety standards and efficiency in industrial operations.
Moreover, machine learning algorithms can analyze vast amounts of data, providing predictive analytics that can foresee potentially dangerous situations before they escalate. This helps organizations act proactively, rather than reactively, enhancing the safety of workers significantly.
Conclusion
The calibration of H2S monitors is a paramount activity that underpins the safety of workers in environments at risk of exposure to hydrogen sulfide. Through understanding the importance of H2S monitor calibration, implementing best practices, and keeping an eye on future technological developments, organizations can ensure the highest standards of health and safety.
At H2S Online Training, we are committed to providing quality educational services in special education, helping spread essential information about hazardous material handling, and how to protect oneself in such environments. Ensuring that businesses remain compliant and workers are safe should always be a priority, and proper calibration of H2S monitors plays a vital role in that mission.