The Importance of Electrical Plastic Molding in Modern Manufacturing
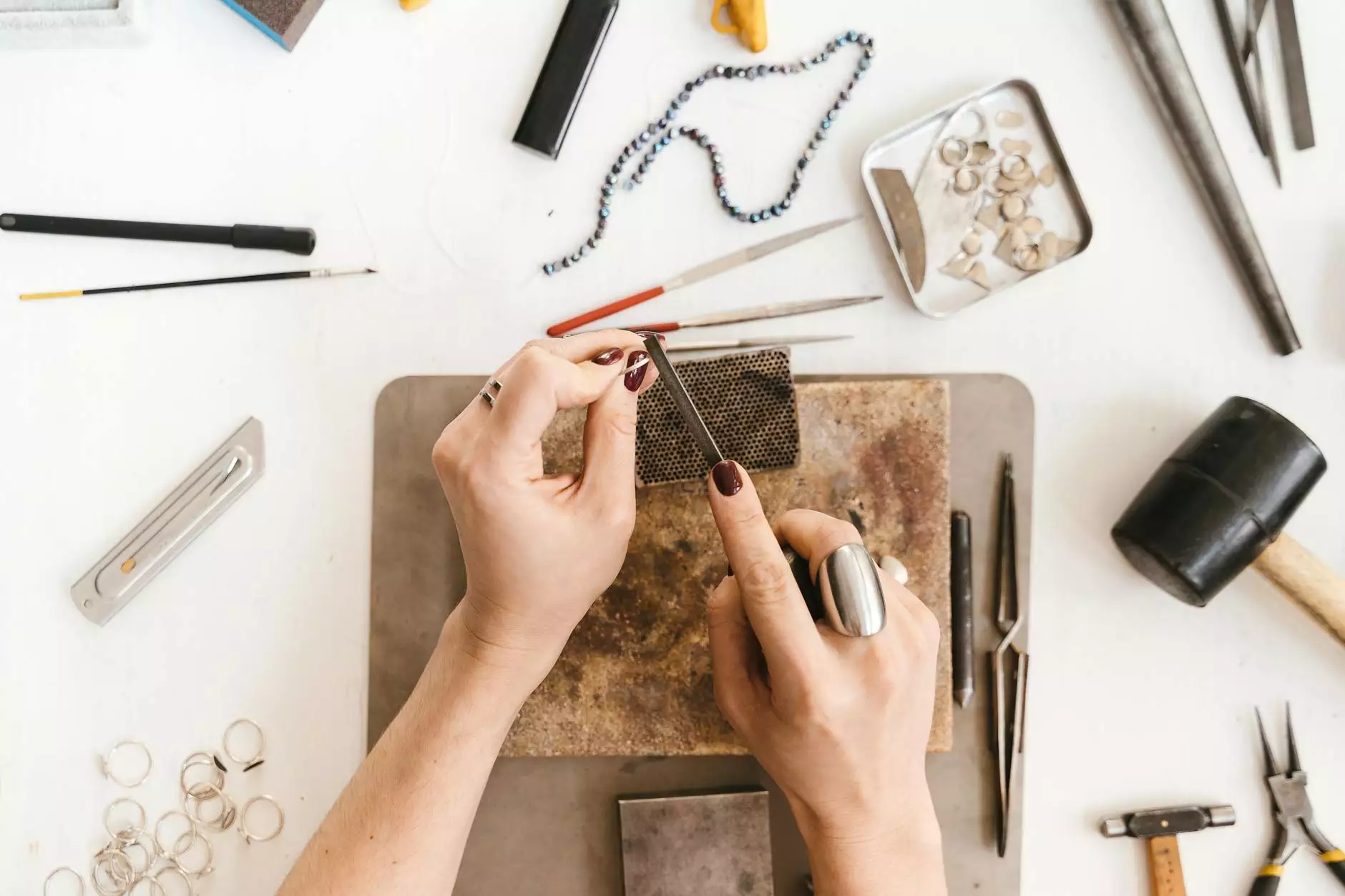
Electrical Plastic Molding has emerged as a pivotal process in the manufacturing sector, enabling businesses to create precision-engineered components crucial for various applications. The evolution of manufacturing processes has opened doors for innovative solutions, and plastic molding stands at the forefront. In this article, we delve into the nuances of Electrical Plastic Molding, exploring its benefits, applications, and the technology that drives it forward.
Understanding Electrical Plastic Molding
At its core, Electrical Plastic Molding is a manufacturing process that involves shaping plastic materials into specific forms using heat and pressure. This process is intricate and requires a deep understanding of both material science and engineering principles. The technology has advanced significantly over the years, leading to better quality, efficiency, and versatility in creating components.
The Process of Electrical Plastic Molding
The process of Electrical Plastic Molding can be broken down into several distinct steps:
- Material Selection: Choosing the right type of plastic is essential. Materials such as ABS, PVC, and polycarbonate are commonly used due to their excellent moldability properties.
- Mold Design: This includes the creation of molds that dictate the final shape and features of the product. Advanced CAD software is typically employed during this phase.
- Heating and Injection: The plastic material is heated until it reaches a molten state and then injected into the mold. This step requires precise temperature control.
- Cooling: Once the mold is filled, cooling mechanisms ensure the plastic solidifies in the desired shape.
- Demolding: The finished product is ejected from the mold, completing the molding cycle.
Advantages of Electrical Plastic Molding
Electrical Plastic Molding offers numerous advantages that have made it a preferred choice for manufacturers worldwide:
- Cost-Effectiveness: The mass production capabilities of plastic molding make it a cost-effective solution for large-scale manufacturing. The efficiency of the process contributes significantly to reduced production costs.
- Precision and Consistency: With the right mold design, companies can achieve high precision and replicate products consistently, ensuring quality control in production.
- Design Flexibility: The molding process allows for complex shapes and designs that may not be feasible with other manufacturing methods.
- Material Versatility: A wide range of plastics can be utilized, enabling manufacturers to choose materials that best suit the performance requirements of their products.
- Shorter Lead Times: The speed of the molding process combined with modern technology enables quicker turnaround times in product development.
Applications of Electrical Plastic Molding
The application of Electrical Plastic Molding spans across various industries, showcasing its versatility and reliability:
1. Automotive Industry
The automotive sector relies heavily on plastic molding for the production of parts such as dashboards, panels, and even engine components. The lightweight properties of molded plastics help improve fuel efficiency.
2. Consumer Electronics
With the demand for electronics growing, manufacturers utilize Electrical Plastic Molding for creating casings, button interfaces, and other intricate components that are both aesthetically appealing and functional.
3. Medical Devices
The medical industry benefits from the precise and sterile production capabilities offered by plastic molding. Items such as syringes, surgical trays, and housings for electronic devices are produced using this technique.
4. Packaging
Plastic molding plays a critical role in forming packaging solutions that are not only lightweight and durable but also customizable for brands seeking unique packaging styles.
5. Electrical Components
Electrical Plastic Molding is particularly significant in creating housings and insulating components for electrical applications, ensuring safety and durability in operations.
Innovations in Electrical Plastic Molding
As technology progresses, the field of Electrical Plastic Molding continues to innovate. Recent advancements include:
1. 3D Printing Integration
3D printing advancements are being integrated with traditional molding techniques to create prototype molds quickly. This synergy allows for rapid prototyping and testing of new designs before full-scale production.
2. Sustainable Practices
Manufacturers are increasingly adopting sustainable practices, utilizing recycled plastics and exploring biodegradable materials to minimize environmental impact while maintaining quality.
3. Smart Manufacturing
The rise of Industry 4.0 has seen the integration of IoT devices in molding machinery. This enables real-time monitoring and predictive maintenance, significantly enhancing production efficiency.
Challenges in Electrical Plastic Molding
While there are numerous benefits to Electrical Plastic Molding, there are challenges that manufacturers face:
1. Material Limitations
Despite the versatility of plastics, not all materials are suitable for every application. Manufacturers must carefully select materials to ensure they meet specific performance criteria.
2. Initial Investment
The upfront costs associated with mold creation can be significant, which may deter smaller companies from pursuing larger production runs.
3. Quality Control
Maintaining consistent quality can be challenging, particularly when it comes to large volume production. Skilled operators and strict processes must be in place to ensure product integrity.
Conclusion: The Future of Electrical Plastic Molding
In conclusion, Electrical Plastic Molding remains a cornerstone of modern manufacturing. Its efficiency, versatility, and ability to adapt to various applications make it indispensable across multiple industries. As innovations continue to shape this field, the future of electrical plastic molding looks promising. Manufacturers who embrace these advancements will not only improve their operational efficiencies but also lead the charge toward sustainable manufacturing practices.
For companies looking to stay competitive, partnering with expert providers like Deep Mould can be an excellent step towards leveraging the full potential of Electrical Plastic Molding. From metal fabrication expertise to innovative plastic solutions, the right collaborations can yield remarkable results.